S5A-HH series, High-rigidity structure design.
Mechanical-type simultaneous two-axis rotary spindle. Warm and gear transmission for B and C axes. Self-made heavy-cutting two-stage switch gear box design. Maximum torque: 1155 N-m.
Suitable for machining the work piece made by Titanium alloy and hard-to-cut material.
Suitable for machining the work piece made by Titanium alloy and hard-to-cut material.
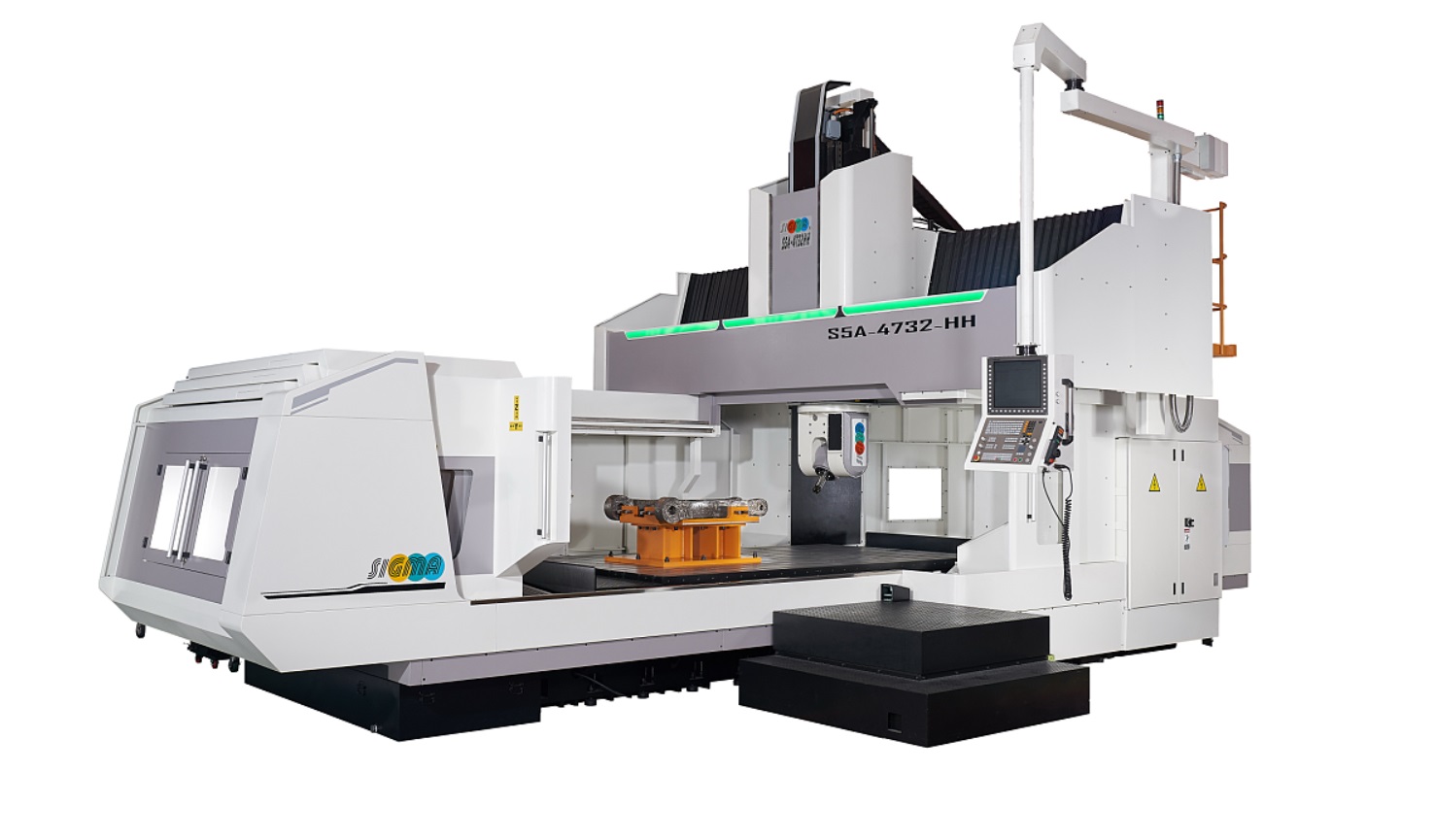
High-rigid structure design.
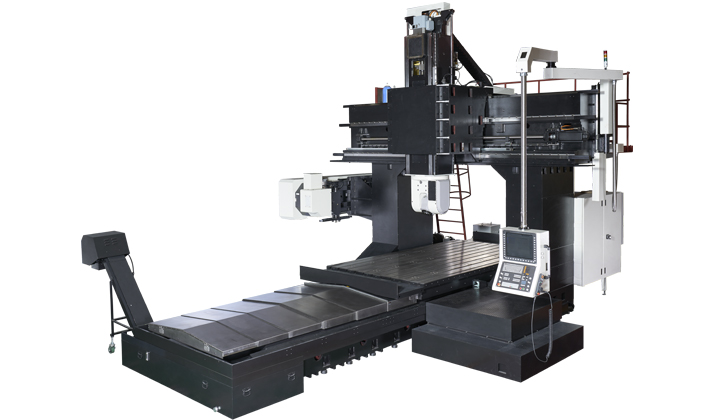
Unique patented design of the four roller-type linear guide ways in the z-axis spindle slide structure.
The z-axis spindle system adopts the box- and roller-type four linear guide ways (model RG45) and is equipped with two close-loop oil pressure balancing units. These specific designs greatly enhance the spindle rigidity and reduce the vibration during machining.
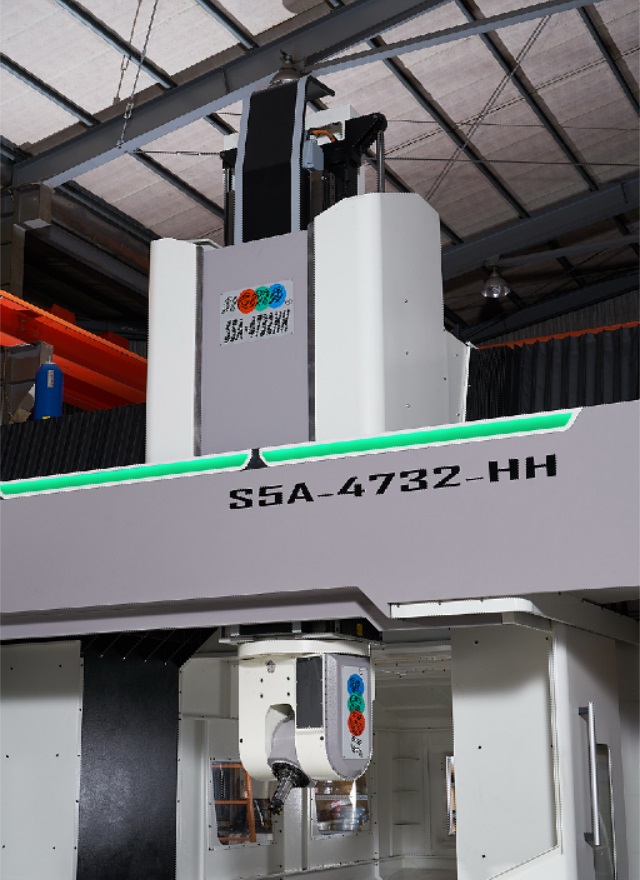
Patented structure design of three roller-type linear guide ways.
The y-axis system adopts three roller-type linear guide ways (model RG45) between spindle and its seat. This design adopts the mixed arrangement of vertical and horizontal guide ways, which may enhance the y-axis movement rigidity and stability.
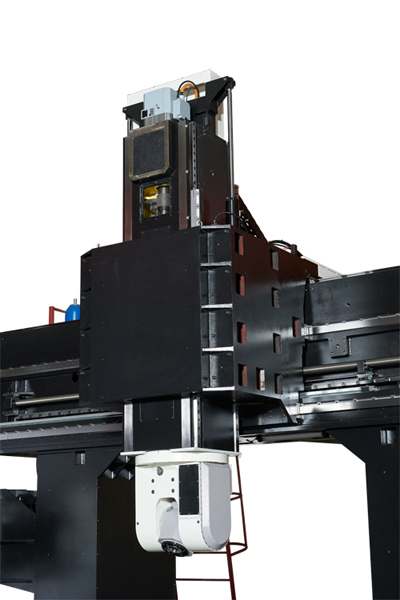
Fully splash guarding metal sheet cover design.
Super large and wide working door design. Fashionable aesthetic and ergonomic safe metal sheet cover design.
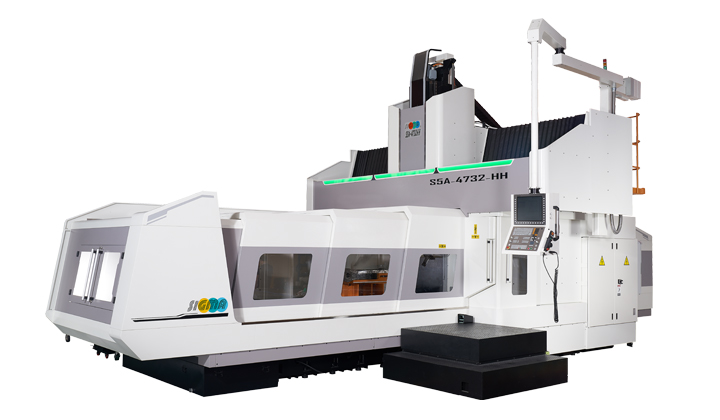
Specific design of safety guardrail upon the cross column. Convenient for machine maintenance.
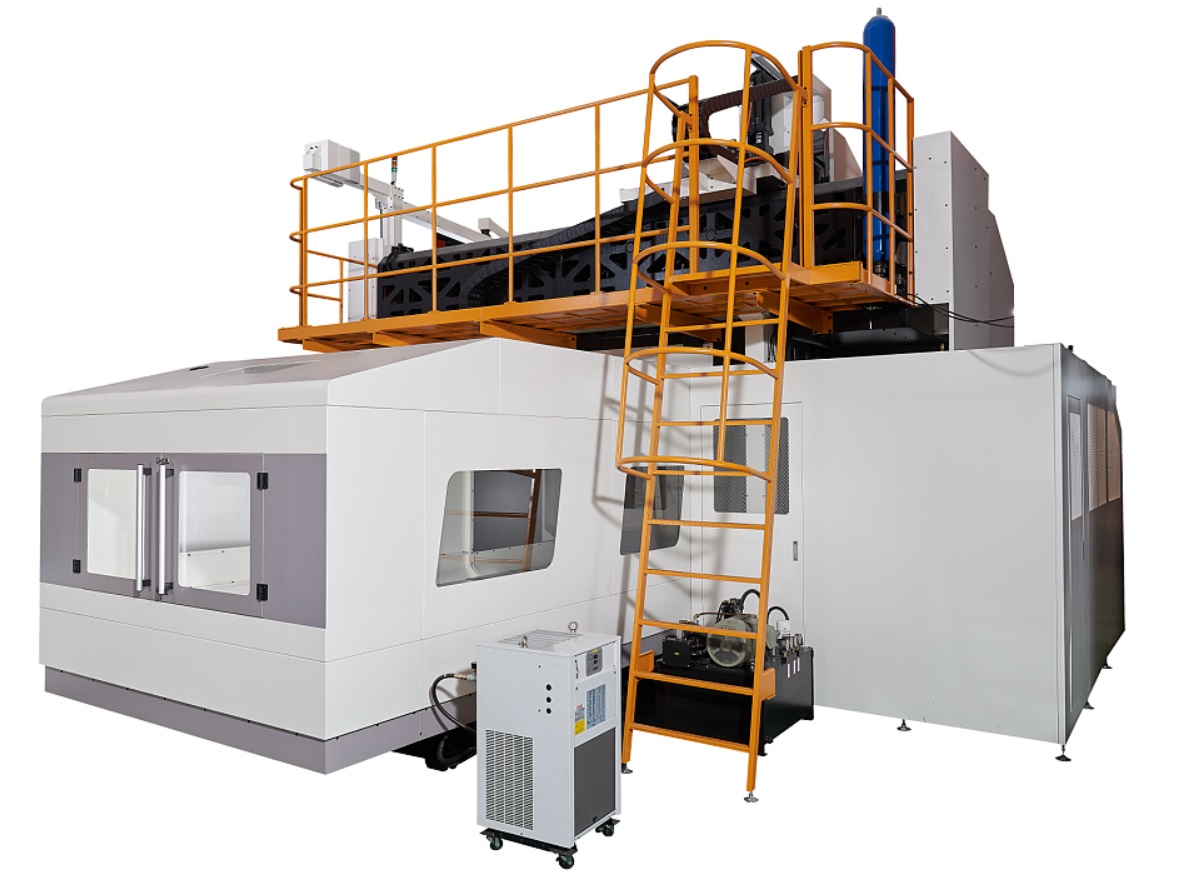
Auto Tool Length & Diameter Measuring system Auto Touch Probe System (optional)
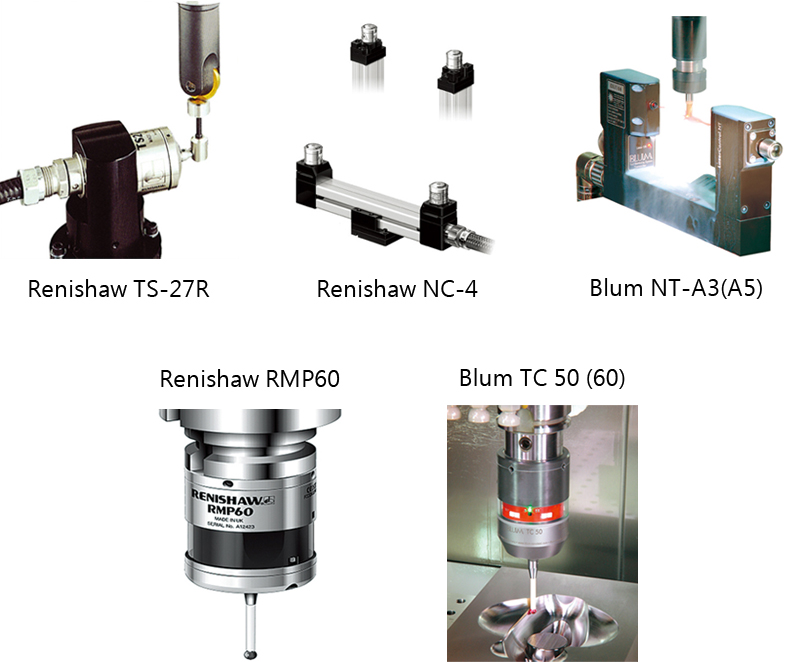